Breakthroughs in coating rate, cathode lifetime,
reliability and simplicity have been achieved.
Deposition rate has doubled. Cathode lifetime is increased to over 10 hours. Parts counts have been reduced and maintenance simplified.
Uniformity over large areas and high coating rates in a
commercial coater is achieved using multiple sources:
Maintenance is simplified using easy to change Baffling cartridges:
High Efficiency Means Practical Deposition Rates.
How is efficiency determined? We measured the total amount of coating deposited by the Radial Arc versus an equivalent unfiltered arc source. The Radial Arc coating volume was 70% of the unfiltered arc coating (see below). Other filters manage only 25% efficiency.
High Rates - 208Angs/s for Chromium:
The plasma divergence and the resulting deposition profiles are easy to adjust (also using permanent magnets) to provide uniformity on stationary or rotating substrates:
Focused Plasma Unfocused Plasma
Deposition Uniformity on Stationary Substrates (wafer, for example):
Practical coating rates in large industrial chambers is provided for using multiple Radial Arc sources.
The plasma from multiple Radial Arc sources following the magnetic field lines and linking up across the vacuum chamber:
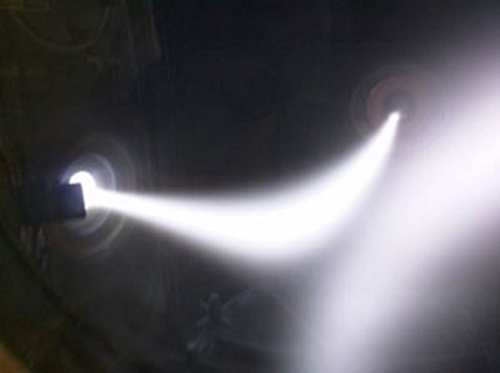
3µm/hr chromium in a 1m industrial coating system on a rotating substrate from 4 Radial Arc sources offset 100mm from each other:
A 70mm offset provides 3% uniformity and 4µm/hr:
Uniformity over any length of substrate (2m shown below) is provided for by simply adding Radial Arc sources:
How Well Are Macroparticles Filtered Out?
Radial Arc titanium coating (10min. 140A):
Radial Arc ta-C coating (8min. 140A):